Tecnology
TESTED SYSTEM
Devulcanization
The different way to recycle
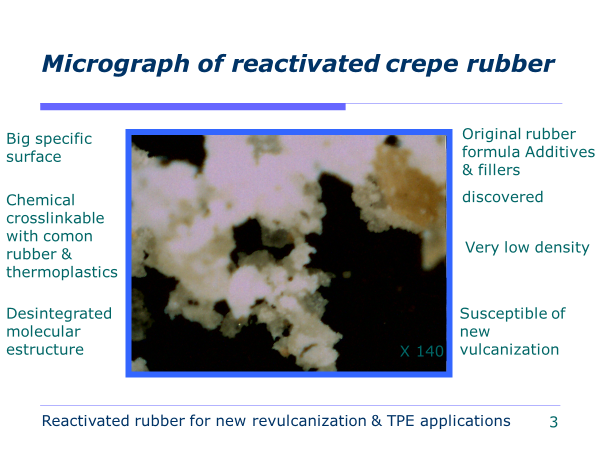
- ADDING VALUE
Could manufactured new fresh rubber batches using same rubber.
The rubber or TPE produced are stable in most cases meets with required specifications including on automotive applications.
Frankly and clear cost savings. Between three to five times less.
- Can be manufactured with any type of reactivated waste rubber.
- Applicability SBR,NBR, EPDM and inclusive with fluoroelastomers.
It has the same applicability as the normal virgin rubber used
- ADDING VALUE
WE HAVE THE TECHNOLOGY
- A new devulcanization system
- At effective costs.
- Full broken molecular crosslink.
- Technology 100 % made in Spain.
- 10 years of study and experience.
- Patented system and technology.
- Capable to reactivate all type of rubbers making possible new re-vulcanization and mix in thermoplastic applications.
- Material obtained is compatible with all rubbers asphalt bitumen and most types of thermoplastics
- Compatibility and stability are excellent.
- The cost does not fluctuate with oil rates.
- The TPE obtained is capable to be recycled again. That meets with environmental best procedures
- Especially useful for applications in automotive parts in injection molding. TPE produced is particularly suitable for shock absorption as down as high temperatures, withstand pressures etc..